Prof. Dr.-Ing. Stefan Soter
Kontakt:
Rainer-Gruenter-Str. 21
42119 Wuppertal
Raum: FH.01.07
Stefan.Soter[at]uni-wuppertal.de
+49 202 439 1950
Termine oder Anfragen bitte über mein
Sekretariat
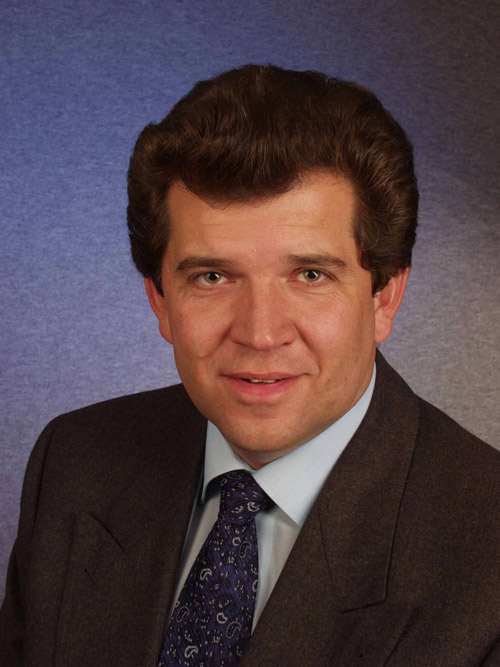
Persönlicher Werdegang
10/1984 bis 11/1989 Universität Bochum; Abschluß: Dipl.-Ing. Elektrotechnik
01/1990 bis 04/1996 FernUniversität Hagen Institut Solatec (Prof. Dr.-Ing. D. Hackstein)
01/1994 Promotion zum Dr.-Ing der Elektrotechnik
Thema der Dissertation: "Systemtechnik für photovoltaisch gespeiste Asynchronmaschinen zum Antrieb von Wasserpumpen"
05/1996 bis 03/2007 Technische Universität Dortmund (Prof. Dr.-Ing. Dr.-Ing. S. Kulig) Lehrstuhl für Elektrische Antriebe und Mechatronik, vormals Lehrstuhl für Elektrische Maschinen, Antriebe und Leistungselektronik
wissenschaftlicher Assistent, Oberingenieur (ab 07/1997), Akademischer Rat (ab 03/2001), Akademischer Oberrat (ab 03/2004)
seit 04/2007 freiberuflicher Leiter von Industrieprojekten in Kooperation mit der Bergischen Universität Wuppertal, Lehrstuhl für Elektrische Maschinen und Antriebe, Prof. Dr.-Ing. Ralph Kennel
04/2005 Angebot der W3-Vertretungsprofessur "Leistungselektronik" der Helmut-Schmidt-Universität Hamburg
ab 10/2008 Lehrauftrag an der Rheinisch-Westfälischen Technischen Hochschule Aachen (RWTH) (Prof. Dr.-Ing. Dr. h.c. dr hab. Kay Hameyer) Institut für Elektrische Maschinen. Titel der Vorlesung: Aufbau und Netzbetrieb von Windkraftanlagen
10/2008 bis 02/2010 W3-Vertretungsprofessur für "Elektrische Maschinen und Antriebe" der Bergischen Universität Wuppertal
ab 03/2010 W3-Professur für "Elektrische Maschinen und Antriebe" der Bergischen Universität Wuppertal
Vorlesungen
- Grundlagen der Elektrotechnik III
- Geregelte elektrische Antriebe
- Leistungselektronik
- Windkraftanlagen
Veröffentlichungen
- 39.C. Junge, S. Gruber, F. Budschun and S. Soter, "System analysis and optimization of a pressure control for a hydraulic-Clutch-Brake-Combination actuated with a linear drive" in 2010 IEEE International Conference on Industrial Technology, 2010, pp. 427--432.
Abstract:
This paper deals with the analysis of an electro-hydraulic system and conception of a pressure control. The controlled system consists of a permanet magnet linear actuator, a hydraulic pressure line and a Clutch-Break-Combination (CBC). The linear actuator generates a force which causes the pressure in the hydraulic line. Depending on the system-pressure, the Clutch-Brake-Combination brakes or clutches with a different torque. Because of the integrated prestressed springs of the CBC, the controlled system is very nonlinear. In addition there are different disturbances, which makes it hardly controllable. The linear actuator is driven with a standard inverter. - 38.A. Bartsch, S. Gruber, R. Wegener and S. Soter, "Testbench for electrical drive systems in hybrid applications" in 2010 IEEE International Conference on Industrial Technology, 2010, pp. 1136--1140.
Abstract:
This paper deals with the development of a test bench for mild hybrid drives used in construction machines. Due to the special conditions under which construction machines are operating this test bench needs to be adapted. Hence the bearing of the electrical drive, which is mounted directly to the internal combustion engine, the temperature control by a cooling circuit and the integration of an appropriate inverter as well as an electrical drive to complete the system are defining the specific requirements of the test bench. These circumstances also affect the measurements and have to be considered during the evaluation of the results. - 37.F. Senicar, C. Junge, S. Gruber and S. Soter, "Zero sequence current elimination for dual-inverter fed machines with open-end windings" in IECON 2010 - 36th Annual Conference of the IEEE Industrial Electronics Society, 2010, pp. 853--856.
ISBN: 1553-572X
Abstract:
A dual-inverter allows to increase easily the maximum available power of a given inverter. When connecting two equal inverters to a machine with open end windings, the available power will raise by factor $\surd$3. However, the dual inverter also introduces a new degree of freedom for the current, which is the zero component current. The dual inverter is known for developing zero component currents, which have three times the frequency of the fundamental current, and can be of a rather large amplitude. This paper analyses the origin of these zero component currents and shows an example of how to eliminate them. Moreover it shows the possibility to suppress zero component currents by using only software algorithms modifying the current control loop. There is no need for extra components. Moreover there are no drawbacks in the quality of control as well as regarding the maximum available voltage. - 36.R. Wegener, S. Gruber and S. Soter, "Development of a low cost embedded diagnosis system for servo controlled drives including data mining technologies" in 2009 IEEE 18th International Symposium on Industrial Electronics (ISIE), 2009, pp. 373--377.
Abstract:
This paper deals with an embedded diagnosis device which improves the reliability of a machine including servo controlled drives by monitoring the system parameters and detecting abnormalities and creeping changes. The detection algorithm is based on data mining technologies, well known in business administration. The presented system consists of a low cost processor board with an SD-card slot for data storage and a field bus connection and is completely independent of the main machine control. The additional benefits are online monitoring possibilities and the storage of the process variables in a high efficient way during the complete lifetime of the machine. - 35.S. Gruber, C. Junge, F. Senicar and S. Soter, "Optimization of a high force tubular linear drive concept with discrete wound coils to fulfill safety standards in industrial applications" in 2009 IEEE Energy Conversion Congress and Exposition, 2009, pp. 2431--2435.
Abstract:
This paper deals with the next step of development of a tubular permanent magnet linear drive concept for industrial applications up to 3000 N thrust force where low cogging forces are required to fulfill safety standards. The presented linear drive concept is designed for easy production and assembly of a few hundred units per year. It can be manufactured on standard production machines because all ferromagnetic parts are made of standard not-laminated steel. This results in a very economic product. Further more the drive concept includes an internal low cost position sensor based on the hall-effect. The different steps of development are proven by measurements of thrust and cogging forces of different prototypes. - 34.C. Junge, F. Senicar, R. Wegener and S. Soter, "Pressure control of a nonlinear system with a linear-PMSM and a standard inverter" in 2009 IEEE International Electric Machines and Drives Conference, 2009, pp. 83--88.
Abstract:
This paper deals with a high dynamic hydraulic pressure control. The pressure is generated by an inverter driven linear drive which applies a force on a hydraulic cylinder. The linear drive has to generate a pressure profile into the hydraulic system and has to keep it at a constant value after reaching the demanded pressure. The controlled system, containing hydraulic oil, dissolved air and overall three spring packs, is showing a highly non-linear characteristic. The control cascade of the inverter is based on a standard position control loop, which is enhanced by a PI based pressure controller, a dynamically adapted position feed-forward and an active anti-windup of the controller in order to provide optimal control behavior of the nonlinear system. - 33.S. Soter, "Wind Converters and Farms -- Technologies and Control", Electrical Energy Systems -- University Enterprise Training Partnership, vol. 2008, no. 4, 2008.
- 32.R. Wegener, S. Gruber, K. Nötzold, F. Senicar, C. Junge and S. Soter, "Development and Test of a High Force Tubular Linear Drive Concept with Discrete Wound Coils for Industrial Applications" in 2008 IEEE Industry Applications Society Annual Meeting, 2008, pp. 1--5.
ISBN: 0197-2618
Abstract:
This paper deals with the development of a tubular permanent magnet linear drive with radial magnetized armature and discrete wound coils mounted on a star-shaped stator part. The rated force of the developed machine is 500 N per segment. This presented particular design results in a very economic product because all primary parts, except of the permanent magnets and coils, are made of standard non-laminated steel and are optimized for easy production and assembly. The control of this machine with a specially built low cost linear sensor based on the Hall-effect is also presented. The suitability of the design is proven by the demonstration of a prototype with measurements of thrust and cogging force. - 31.R. Wegener, S. Gruber, K. Nötzold and S. Soter, "Optimization of a Low-Cost Position Sensor for a Permanent Magnet Linear Drive" in PCIM Asia 2008, 2008.
- 30.T. Rösmann and S. Soter, "Regenerative Operation of DC-Series Machines in Pitchsystems for Multimegawatt Windturbines" in 2008 IEEE Industry Applications Society Annual Meeting, 2008, pp. 1--7.
ISBN: 0197-2618
Abstract:
Modern windmills and multimegawatt turbines are nearly exclusively equipped with electrical pitchsystems.The pitchsystem itself has to fulfill the following functions: In the case of strong wind conditions during normal operation, the system is responsible to limit the generator torque. On the other hand, the feathering position of the blades is needed to brake down the turbine in stop or emergency situations. In modern windturbines this aerodynamical brake is necessary, because the mechanical brake is designed as a holding brake and is not able to prevent overspeed conditions. The last function described is safety relevant. Because of this, pitch systems are equipped with an backup energy storage. So the blade can be put into feathering position in any case. DC-machines are preferred in pitch systems because of their capability to be supplied directly by the DC-storage unit without any control or powerelectronics. The motor must be designed especially for this battery driven operation because current and speed during emergency battery drive are depending on the mechatronical behaviour of the machine. Actually two different DC machine types are used in pitch systems: DC-series and DC-compound machines. DC- compound machines were introduced because of their natural 4Q operation area. But an actual development allows the regenerative operation also for DC-series machines and makes them very cost attractive for multimegawatt pitchsystems.