Dr.-Ing. Sebastian Gruber
Kontakt:
Rainer-Gruenter-Str. 21
42119 Wuppertal
Raum: FH.01.08
+49 202 439 1123
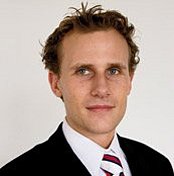
Persönlicher Werdegang
Abitur 1997 in Schwerte
Ausbildung 1998-2001 zum Energieelektroniker Fachrichtung Anlagentechnik bei der Siemens AG
Studium der ET an der Universität Dortmund 10/2001-07/2006
07/2006-04/2007 wissenschaftlicher Mitarbeiter am Lehrstuhl für Elektrische Antriebe und Mechatronik an der Universitat Dortmund
seit April 2007 wissenschaftlicher Mitarbeiter am Lehrstuhl für Elektrische Maschinen und Antriebe an der Bergischen Universitat Wuppertal
Vorlesungen
Veröffentlichungen
- 7.C. Junge, S. Gruber, F. Budschun and S. Soter, "System analysis and optimization of a pressure control for a hydraulic-Clutch-Brake-Combination actuated with a linear drive" in 2010 IEEE International Conference on Industrial Technology, 2010, pp. 427--432.
Abstract:
This paper deals with the analysis of an electro-hydraulic system and conception of a pressure control. The controlled system consists of a permanet magnet linear actuator, a hydraulic pressure line and a Clutch-Break-Combination (CBC). The linear actuator generates a force which causes the pressure in the hydraulic line. Depending on the system-pressure, the Clutch-Brake-Combination brakes or clutches with a different torque. Because of the integrated prestressed springs of the CBC, the controlled system is very nonlinear. In addition there are different disturbances, which makes it hardly controllable. The linear actuator is driven with a standard inverter. - 6.A. Bartsch, S. Gruber, R. Wegener and S. Soter, "Testbench for electrical drive systems in hybrid applications" in 2010 IEEE International Conference on Industrial Technology, 2010, pp. 1136--1140.
Abstract:
This paper deals with the development of a test bench for mild hybrid drives used in construction machines. Due to the special conditions under which construction machines are operating this test bench needs to be adapted. Hence the bearing of the electrical drive, which is mounted directly to the internal combustion engine, the temperature control by a cooling circuit and the integration of an appropriate inverter as well as an electrical drive to complete the system are defining the specific requirements of the test bench. These circumstances also affect the measurements and have to be considered during the evaluation of the results. - 5.F. Senicar, C. Junge, S. Gruber and S. Soter, "Zero sequence current elimination for dual-inverter fed machines with open-end windings" in IECON 2010 - 36th Annual Conference of the IEEE Industrial Electronics Society, 2010, pp. 853--856.
ISBN: 1553-572X
Abstract:
A dual-inverter allows to increase easily the maximum available power of a given inverter. When connecting two equal inverters to a machine with open end windings, the available power will raise by factor $\surd$3. However, the dual inverter also introduces a new degree of freedom for the current, which is the zero component current. The dual inverter is known for developing zero component currents, which have three times the frequency of the fundamental current, and can be of a rather large amplitude. This paper analyses the origin of these zero component currents and shows an example of how to eliminate them. Moreover it shows the possibility to suppress zero component currents by using only software algorithms modifying the current control loop. There is no need for extra components. Moreover there are no drawbacks in the quality of control as well as regarding the maximum available voltage. - 4.R. Wegener, S. Gruber and S. Soter, "Development of a low cost embedded diagnosis system for servo controlled drives including data mining technologies" in 2009 IEEE 18th International Symposium on Industrial Electronics (ISIE), 2009, pp. 373--377.
Abstract:
This paper deals with an embedded diagnosis device which improves the reliability of a machine including servo controlled drives by monitoring the system parameters and detecting abnormalities and creeping changes. The detection algorithm is based on data mining technologies, well known in business administration. The presented system consists of a low cost processor board with an SD-card slot for data storage and a field bus connection and is completely independent of the main machine control. The additional benefits are online monitoring possibilities and the storage of the process variables in a high efficient way during the complete lifetime of the machine. - 3.S. Gruber, C. Junge, F. Senicar and S. Soter, "Optimization of a high force tubular linear drive concept with discrete wound coils to fulfill safety standards in industrial applications" in 2009 IEEE Energy Conversion Congress and Exposition, 2009, pp. 2431--2435.
Abstract:
This paper deals with the next step of development of a tubular permanent magnet linear drive concept for industrial applications up to 3000 N thrust force where low cogging forces are required to fulfill safety standards. The presented linear drive concept is designed for easy production and assembly of a few hundred units per year. It can be manufactured on standard production machines because all ferromagnetic parts are made of standard not-laminated steel. This results in a very economic product. Further more the drive concept includes an internal low cost position sensor based on the hall-effect. The different steps of development are proven by measurements of thrust and cogging forces of different prototypes. - 2.R. Wegener, S. Gruber, K. Nötzold, F. Senicar, C. Junge and S. Soter, "Development and Test of a High Force Tubular Linear Drive Concept with Discrete Wound Coils for Industrial Applications" in 2008 IEEE Industry Applications Society Annual Meeting, 2008, pp. 1--5.
ISBN: 0197-2618
Abstract:
This paper deals with the development of a tubular permanent magnet linear drive with radial magnetized armature and discrete wound coils mounted on a star-shaped stator part. The rated force of the developed machine is 500 N per segment. This presented particular design results in a very economic product because all primary parts, except of the permanent magnets and coils, are made of standard non-laminated steel and are optimized for easy production and assembly. The control of this machine with a specially built low cost linear sensor based on the Hall-effect is also presented. The suitability of the design is proven by the demonstration of a prototype with measurements of thrust and cogging force. - 1.R. Wegener, S. Gruber, K. Nötzold and S. Soter, "Optimization of a Low-Cost Position Sensor for a Permanent Magnet Linear Drive" in PCIM Asia 2008, 2008.