Dr.-Ing. Sebastian Gruber
Contact:
Rainer-Gruenter-Str. 21
42119 Wuppertal
room: FH.01.08
ralf.wegener[at]uni-wuppertal.de
+49 202 439 1123
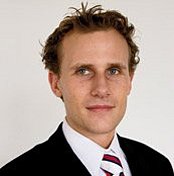
Personal career
High school diploma 1997 in Schwerte
Apprenticeship 1998-2001 as power electronics technician specializing in systems engineering at Siemens AG
Studies of ET at the University of Dortmund 10/2001-07/2006
07/2006-04/2007 research associate at the Chair of Electrical Drives and Mechatronics at the University of Dortmund
since April 2007 research associate at the Chair of Electrical Machines and Drives at the University of Wuppertal
Lectures
Publications
- 17.R. Wegener, S. Gruber and S. Soter, "Automated Workflow for Creating Lecture Videos from LaTeX Beamer Slides", EDULearn 2025, Palma Spain, Jun. 2025.
Abstract:
An automated workflow for the creation of instructional videos from LaTeX documents is described. For this purpose, a new latex extension is developed, that uses open-source software and an AI-based text-to-speech synthesizer to convert the explanatory text into audio and to edit it together with the lecture slides into a video. By automating the process, subsequent changes can be made very easily, allowing all materials to be revised at any time with minimal effort. Video subtitles can also be generated automatically to ensure accessibility. - 16.S. Gruber, "Analyse und Optimierung eines tubularen Linearmotors in Sonderbauform für hydraulisch betätigte Kupplungs-Brems-Kombinationen", {Bergische Universität Wuppertal}, 2016.
- 15.S. Gruber, R. Wegener and S. Soter, "Design Process for High Force Tubular Linear Drive with DiscreteWound Coils" in The 10th International Symposium on Linear Drives for Industry Applications, 2015.
- 14.B. Krüger, S. Gruber and S. Soter, "Controlling of medium voltage power-factor of photovoltaic power plants from the low voltage side" in 2013 IEEE Energy Conversion Congress and Exposition, 2013, pp. 569--574.
ISBN: 2329-3748
Abstract:
The effort to make the production of electrical energy much more environmental-friendly, large conventional power plants will be replaced by several smaller regenerative power plants. In order to improve stability and controllability, these smaller power plants are supposed to control the active power, the reactive power and the power factor in the medium voltage grid like conventional power plants. This paper will discuss three different methods to control the medium-voltage power factor from the low voltage side in consideration of parasitic effects from cables and transformers to fulfill the guidelines at the grid connection point. A method with a self-learning-algorithm will be implemented and proven by simulations and measurements on a test bench with inverter and 400 V to 10 kV grid transformer. The self-learning-algorithm will give the opportunity to reach every required power factor at the grid connection point. - 13.S. Gruber, B. Krüger and S. Soter, "High force tubular linear actuator with integrated eddy current brake for spring-loaded systems" in 2013 IEEE AFRICON, 2013, pp. 1--5.
ISBN: 2153-0033
Abstract:
In order to meet safety standards in manufacturing industry many production machines are equipped with safety stop functions based on spring-loaded systems. This paper deals with an integrated eddy current brake of a high force tubular permanent magnet linear actuator for hydraulic applications with small actuating pathes. An analytical description of different design criteria for the integrated eddy current brake are shown. The special not rotational symmetrical design of the tubular linear actuator is transferred to a 2D transient FEM simulation model to predict the braking behavior caused by the spring load in case of an emergency stop. Measurements on a test bench are in good agreement with the simulation results and are used to validate the model. - 12.S. Gruber, R. Wegener and S. Soter, "Detent force reduction of a tubular linear drive by using a genetic algorithm and FEM - verification of simulation results" in IECON 2012 - 38th Annual Conference of the IEEE Industrial Electronics Society, 2012, pp. 1731--1736.
Abstract:
In order to meet industrial safety standards in eccentric presses, the detent force caused by the reluctance change between permanent magnet (PM) and stator teeth of the acting high force tubular permanent magnet linear synchronous machines (PMLSM) should be reduced. The detent force is generated by two components: the slot effect which is already decreased by the closing slot technique and proven in [3] and the end effect which will be optimized by using auxiliary poles at the end of the machine. Therefore a special genetic algorithm (GA) is developed which rates the simulation results of the FEM and produces new auxiliary poles. The combined simulation tries to find an optimal size and position for auxiliary poles to reduce the whole detent force. The numerical calculations propose a minimized detent force caused by the located poles, which is independent from the length of the machines (1 to 5 modules). The result will be proven by measurements. - 11.C. Junge, T. Ruhland, S. Gruber, R. Wegener and S. Soter, "Controlled input-output-shaft synchronisation by a linear drive actuated hydraulic clutch-brake-combination" in 2011 IEEE AFRICON, 2011, pp. 1--5.
Abstract:
The focus of this paper is the control to accelerate and decelerate a drive shaft exactly with a hydraulic clutch-brake-combination (CBC). The CBC is actuated by a permanent magnet linear synchronous machine (PMLSM) with an integrated hydraulic cylinder. The servo-converter-controlled-PMLSM is able to generate the pressure for the CBC. A superposed control cascade with a pressure control and a special synchronization control is implemented to vary the transmitted torque and therefore the accurate acceleration and deceleration of the drive shaft within a preset angle. This development ensures a controlled synchronization of the input-output shaft by a CBC in a specific point of time within a preset mechanical angle. - 10.S. Gruber, C. Junge, R. Wegener and S. Soter, "Overview of a special Developed Linear Drive Concept with integrated Hydraulic Cylinder für Clutch-Brake-Combinations in Eccentric Presses" in Proceedings / LDIA 2011, the Eighth Symposium on Linear Drives for Industry Applications, July 3 - 6, 2011, Eindhoven, The Netherlands, Eindhoven: {TU Eindhoven}, 2011.
ISBN: 978-90-386-2524-9
- 9.C. Prasse, A. Kamagaew, S. Gruber, K. Kalischewski, S. Soter and M. Hompel, "Survey on energy efficiency measurements in heterogenous facility logistics systems" in 2011 IEEE International Conference on Industrial Engineering and Engineering Management, 2011, pp. 1140--1144.
ISBN: 2157-362X
Abstract:
Basically there are two ways to improve the energy efficiency of heterogeneous material flow systems - modification of technical components and control with intelligent strategies. In order to reduce the consumed energy the design, configuration and control strategy of different conveyor systems have to be analyzed by mechanical and electrical measurements. To quantify the need of energy under conditions as close as possible to reality a testing facility with different conveyor elements and electrical drives with power monitoring capabilities was installed in order to give a database for further research activities. On the one hand the acquired data can be used to optimize the efficiency of the total drive train. On the other hand they conduce to develop new intelligent control strategies for an energy efficient operation of heterogeneous facility logistics system. Eventually, the design of a monitoring system in a testing facility is the topic of this contribution. - 8.S. Gruber, C. Junge, R. Wegener and S. Soter, "Reduction of detent force caused by the end effect of a high thrust tubular PMLSM using a genetic algorithm and FEM" in IECON 2010 - 36th Annual Conference of the IEEE Industrial Electronics Society, 2010, pp. 968--973.
ISBN: 1553-572X
Abstract:
In order to meet industrial safety standards in eccentric presses, the detent force of the acting high force tubular permanent magnet linear synchronous machines (PMLSM) should be reduced. The detent force is caused by two components: the slot effect and the end effect. Both effects are based on the reluctance change between permanent magnet (PM) and stator teeth. The slot effect is already optimized by the closing slot technique which is proven by measurements presented in this paper. The main topic is the reduction of detent force by using auxiliary poles at the end of the machine. Therefore a special genetic algorithm (GA) is developed which rates the simulation results of the FEM and produces new auxiliary poles. The combined simulation tries to find an optimal size and position for auxiliary poles to reduce the whole detent force. The numerical calculations propose a minimized detent force caused by the located poles, which is independent from the length of the machines (2, 3 or 5 modules).