Dr.-Ing. Ralf Wegener
Contact:
Rainer-Gruenter-Str. 21
42119 Wuppertal
Room: FH.01.01
ralf.wegener[at]uni-wuppertal.de
+49 202 439 1462
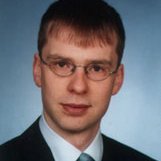
Personal career
High school diploma 1996
Studies of electrical engineering at the University of Dortmund from 1997 to 2002
Scientific employee at the University of Dortmund from August 2002 to July 2008
From August 2008 scientific employee at the University of Wuppertal
Since 2012 academic councilor at the University of Wuppertal
Since 2015 Akademischer Oberrat at the University of Wuppertal
Lectures
Publications
- 10.R. Wegener,Zylindrischer Linearmotor mit konzentrierten Wicklungen für hohe Kräfte: Dortmund, Techn. Univ., Diss., 2008. Norderstedt: {Books on Demand}, 2008.
- 9.R. Wegener, S. Gruber, K. Nötzold, F. Senicar, C. Junge and S. Soter, "Development and Test of a High Force Tubular Linear Drive Concept with Discrete Wound Coils for Industrial Applications" in 2008 IEEE Industry Applications Society Annual Meeting, 2008, pp. 1--5.
ISBN: 0197-2618
Abstract:
This paper deals with the development of a tubular permanent magnet linear drive with radial magnetized armature and discrete wound coils mounted on a star-shaped stator part. The rated force of the developed machine is 500 N per segment. This presented particular design results in a very economic product because all primary parts, except of the permanent magnets and coils, are made of standard non-laminated steel and are optimized for easy production and assembly. The control of this machine with a specially built low cost linear sensor based on the Hall-effect is also presented. The suitability of the design is proven by the demonstration of a prototype with measurements of thrust and cogging force. - 8.R. Wegener, S. Gruber, K. Nötzold and S. Soter, "Optimization of a Low-Cost Position Sensor for a Permanent Magnet Linear Drive" in PCIM Asia 2008, 2008.
- 7.S. Soter and R. Wegener, "Development of Induction Machines in Wind Power Technology" in 2007 IEEE International Electric Machines & Drives Conference, 2007, pp. 1490--1495.
Abstract:
This paper gives an overview of the development of the induction machine as a generator for wind turbines from the middle of the 20th century up to now. After a short history chapter the different energy conversion concepts are presented. At first a squirrel cage machine is direct coupled to the grid (Danish concept). To adjust the machine speed the second step is a wound rotor machine with collector rings to change rotor resistance. This concept allows the first adaption of the operating point of the wind turbine and the induction machine. Another concept is to connect the stator of a squirrel cage machine with a full inline voltage source converter to the grid to get the flexibility in rotational speed and to control the reactive power. The doubly fed induction machine is the latest development. This concept uses a bidirectional voltage source converter in the rotor circuit with a rated power of only 30{%} of the rated generator power. Now it is possible to change the rotational speed and the reactive power independently and in a wide range. A generalized control scheme of a modern doubly fed induction machine (DFIG) is shown in the last part to explain the variability and the range of application. Today over 70{%} of the wind turbines are build up with DFIG. - 6.R. Wegener, F. Senicar, C. Junge and S. Soter, "Low Cost Position Sensor for Permanent Magnet Linear Drive" in 2007 IEEE 2nd International Conference on Power Electronics and Drive Systems (PEDS), 2007, pp. 1367--1371.
ISBN: 2164-5264
Abstract:
This paper deals with a custom made low cost sensor for measuring the position of a permanent magnet linear motor. The principle how to measure position and movement direction with two analog hall sensor elements is described. The following simulated and detailed error and failure treatment is very important to know exactly the performance and the possibilities of this low cost sensor element. Afterwards this position sensor is build and some measurements with a linear machine is done. After filtering, the accuracy of the two signals is high enough to be an input of a converter control to determine the correct current which has to be injected. If there is another higher ranking closed-loop control, e.g. pressure, flow or force, in the control system this low cost sensor is sufficient and works very well. It is possible to implement the very small sensor in the housing of the linear drive. This sensor costs less than 15 dollar and can not be compared to a very precise working linear senor for some hundred dollar in order to position the linear drive very exact but the accuracy is high enough to build a lower ranking closed-loop control and to stabilize a complex control system of converter, linear drive and load. - 5.R. Wegener, S. Soter and T. Rösmann, "Facility Employing Standard Converters for Testing DFIG Wind Generators up to 30kW" in 2006 IEEE 15th International Symposium on Industrial Electronics (ISIE), 2006, pp. 1025--1029.
Abstract:
This paper presents a test facility for a double fed induction generator (DFIG) with a rated power of approximately 30 kW. The stator of the machine is directly connected to the grid and the rotor is fed with variable voltage and frequency. Actually such machines are used in wind generators with a power of more than 500 kW with special built converters. In the presented test facility the used converter consists of two standard low cost voltage source converter units with connected DC-link. The firmware of these converters are normally not suitable for feeding the rotor because there are not able to calculate the slip frequency and phase in real time. In the presented solution this is programmed in two application modules plugged into the converter. The equivalent network parameters of the DFIG are determined by the converter. These are necessary for the development of an analytical model of the system to set up a closed loop active and reactive power control. The test system provides the ability to control both power types decoupled and with a linear characteristic - 4.R. Wegener, S. Soter and T. Rösmann, "Operation of double fed induction generators with unmodified low cost standard converters" in 2006 37th IEEE Power Electronics Specialists Conference, 2006, pp. 1--5.
ISBN: 2377-6617
Abstract:
This paper presents how to operate a double fed induction generator (DFIG) with a rated power of approximately 30kW with unmodified low cost standard converters. The stator of the machine is directly connected to the grid and the rotor is fed with variable voltage and frequency from two standard low cost voltage source converters. Actually such machines are used in wind generators with a rated power of more than 500 kW with special build converters. In the presented solution the rotor of the DFIG is fed with two DC-Link connected standard voltage source converters. The original software is designed to calculate speed and phase of the rotor by receiving a speed signal from the rotor shaft. Therefore it is necessary to add two small application modules to modify the firmware externally to realize the calculation of slip frequency and phase in real time. The equivalent network parameters of the DFIG are determined by the converter itself by using an autotune function. With this parameters it is possible to develop an analytical model of the system to set up a closed loop active and reactive power control. The test system provides the ability to control both power types decoupled and with an approximately linear characteristic. - 3.R. Wegener, S. Soter and C. Deipenbrock, "Sensorless Determination of the Exact Rotor Position of a Blocked Permanent Magnet Machine" in PCIM Asia 2006, 2006.
- 2.S. Soter, R. Wegener, J. Dopheide and B. Kiffer, "Low cost vector control for permanent-magnet-synchronmotor with only one DC-link current sensor for pumping application" in IEEE International Conference on Electric Machines and Drives, 2005, 2005, pp. 174--177.
Abstract:
This paper presents a cost-efficient closed loop control of a small permanent magnet machine for pumping application. The special feature of the described solution is only one current probe in the DC-link of the converter. The three phase currents are calculated from this measured current in combination with the state of semiconductors at the time of measurement. Near the sector borders of the space vector modulation the turn-on-time of one semiconductor is too short for measuring the current. A method is developed to compensate these blind areas with the extension of the turn-on-time in half of the PWM-cycles. The measured values are checked by an error detection and exchanged if necessary by an approximation. The position of the rotor is also calculated from the measured current. The paper presents a close loop vector control with less costs than conventional solutions. - 1.R. Lach, S. Soter and R. Wegener, "Experimental determination of systemeigenfrequencies on electrical drives" in 11th International Power Electronics and Motion Control Conference, Riga: {Riga Technical University}, 2004.
ISBN: 9984320588